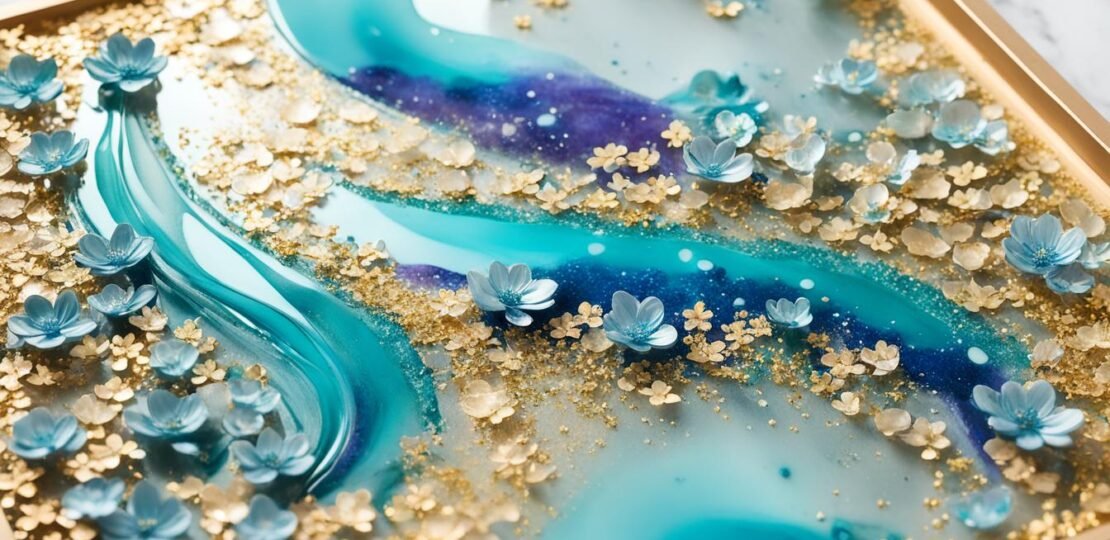
In the vibrant bustle of our studio, where the air is electric with creativity, we stand side by side—my husband, courageously facing the daily tides of agoraphobia, anxiety, and depression, and I, steadfast with the fragility of osteoporosis. These are the dragons we contend with, their formidable presence a constant in our lives. Yet, they do not define us. Instead, they carve out a space for growth, teaching us resilience that transcends the physical, nurturing a spirit that refuses to yield.
We harness our battles as catalysts for creation, pouring resin into moulds just as we pour our souls into overcoming each day’s hurdles. Our studio becomes a sanctuary where the alchemy of epoxy resin transforms into art, and the meticulousness of resin pouring techniques metamorphoses into meditative therapy.
Join us in this space where challenges are merely the beginning of beauty, where resin art and resin crafting become our testament to life’s potential. Support our journey and explore with us at www.devilndove.com, where every creation is a victory, a story, a shared breath.
Key Takeaways
- Resilience is cultivated not only through personal struggle but also through the shared act of creation.
- Pouring resin serves as both an art form and a therapeutic process, aiding us in combatting our mental and physical challenges.
- The right resin pouring technique is essential for achieving professional, flawless results in resin art.
- Mental and physical adversities can coexist with successful crafting and artistic enterprises.
- Our art is our stronghold, providing a space where barriers are transformed into gateways for creative expression.
- Through supportive partnership and artistic craft, we forge a path of healing and triumph.
Unveiling the Art of Epoxy Resin Pouring
At the heart of resin art lies the transformative craft of epoxy resin pouring. This intricate process merges the fluid beauty of art with the meticulous attention of crafting. The magical journey from liquid to solid captures more than just materials—it captures imagination. Whether we are creating delicate pendants or revamping a vintage coffee table, the diverse range of creative projects that can be achieved through crafting with resin is nothing short of inspiring.
Understanding epoxy resin’s unique characteristics is fundamental to mastering its application. Epoxy’s versatility makes it a favourite medium among artists and crafters. When poured, it turns into a solid, transparent form that has the remarkable ability to preserve and showcase the encapsulated treasures within—be it vibrant inks, sparkling glitters, or even natural flora.
“Epoxy resin pouring allows us to seize a moment in time, creating everlasting art that is as durable as it is beautiful.”
- Discover the limitless potential of resin art, where each pour is a new adventure.
- Learn the subtle art of crafting with resin, balancing precision and creativity.
- Delve into the intricacies of epoxy resin pouring and watch art take shape before your eyes.
- Explore creative projects that transform everyday items into extraordinary pieces.
The captivating clarity and gloss of a finished epoxy piece are proof of its maker’s patience and skill. By mastering the techniques and respecting the curing times, we are able to turn our visions into tangible works of art—each with its own story, its own unique blend of colours and elements. For both the novice and experienced crafter alike, the realm of epoxy resin pouring is an open canvas, inviting us to leave our mark on something ever-lasting.
The Importance of Proper Pouring Technique
In our artistic endeavors, we’ve come to recognize that the secret behind a pristine epoxy resin creation lies in the pouring technique. Not only does it set the foundation for the artwork’s longevity, but it also determines the smoothness and clarity of the final piece. Understanding the craft of epoxy resin techniques and implementing the right resin pouring tips can prove to be the difference between a masterpiece and a project plagued with resin imperfections.
Preventing Imperfections in Your Finish
One common frustration artists face when working with resin is the occurrence of air bubbles in resin. To prevent this vexing issue, a meticulous pouring approach is vital. The key is to pour gently and keep the stream of resin close to the surface, thereby reducing the chance for air to be trapped beneath. Additionally, consistent and controlled pressure on the resin container during the pouring process ensures an even and manageable flow that helps in avoiding the formation of unwanted bubbles.
Understanding the Consequences of a Clumsy Pour
A clumsy pour can have dire consequences: from an uneven surface, which mars the aesthetics, to the presence of air bubbles, which compromise the structural integrity of the resin piece. Beyond the visual mishaps, an improper technique can mean wasted material and time. Correcting such mistakes is often a tedious process and sometimes, it’s not quite salvageable, necessitating a complete do-over. Hence, mastering epoxy resin techniques is not just about achieving perfection; it’s also about efficiency and economy of resources.
Utilizing these insights, here’s a quick reference table with targeted resin pouring tips to help you achieve a flawless finish:
Pouring Phase | Technique | Outcome |
---|---|---|
Initial Pour | Keep resin stream close to the surface and pour slowly. | Minimizes air entrapment, reducing potential for bubbles. |
Mid-Pour | Squeeze the resin container to regulate the flow. | Provides better control over resin distribution, avoiding uneven layers. |
Final Spread | Move smoothly and evenly; use a spreader if necessary. | Ensures even coverage and a smooth, perfect surface finish. |
As we continue to explore the world of resin art, we invite you to join us on this journey of perfecting the craft. Embrace these techniques, and your resin pieces will not only radiate beauty but also a standard of quality that sets your work apart in the realm of epoxy resin artistry.
Setting the Stage: Pre-Pour Essentials
Before the exhilarating moment of preparing for a resin pour, there’s a symphony of groundwork that must be orchestrated. Our foundational mantra revolves around ensuring every detail is meticulously attended to, laying the perfect canvas for a mesmerizing resin masterpiece. It’s about harmonizing our space and materials so when the time comes to pour, we’re set for success.
Ensuring a Clean, Dry, and Level Surface
Initiating our pre-pour preparations, a stern evaluation of our surface sets the stage. We revere this step – it’s the bedrock that will cradle the unfolding resin art. Swept free of dust, devoid of moisture, and as level as the horizon, this surface awaits the transformation into lustrous elegance.
Choosing the Right Epoxy Resin for Your Project
In our pursuit of excellence, selecting the right epoxy resin is akin to choosing the finest paints for a masterpiece. Do we reach for a deep pour epoxy, crafting visuals of grandeur and depth, or is a table top epoxy our muse for the day, offering a surface sleek and inviting to the touch? The nuances between them can elevate or inhibit our artistic expression.
Type of Epoxy Resin | Best Use | Viscosity | Max Depth per Pour |
---|---|---|---|
Table Top Epoxy | Coating surfaces (Tables, Coasters, Artwork) | Low to Medium | Up to 1/8 inch |
Casting Resin | Large items encapsulations (Paperweights, Figurines) | Medium to High | Up to 2 inches |
Deep Pour Epoxy | Thick castings (River Tables, Large Molds) | Low | Up to 4 inches |
Prime our canvas, select our medium, and contemplate the potential that lies before us; such are the joys and duties as we tread the path of resin artistry. Now, with hearts alight and hands steady, we move forward to the defining moment of creation – the pour itself.
Resin – How to Pour Resin
As we delve into how to pour resin, it’s essential to acknowledge that the craft requires patience, precision, and a passion for DIY resin projects. Through careful application of proven resin techniques, even beginners can achieve professional-looking results. Let’s explore the step-by-step process of working with epoxy and ensure that your next project is a resounding success.
- Mix the resin and hardener in equal parts to ensure a robust and curing finish.
- Carefully pour the mixture onto your work, taking care not to introduce air bubbles.
- Use spreading tools to guide the epoxy across the surface, achieving an even layer.
- Apply heat to the surface to release any trapped air and perfect the smoothness.
- Allow the work to settle undisturbed, leading to a fully cured piece within 24 hours.
Being well-versed in resin techniques empowers us to craft not just objects, but stories. Every diy enthusiast or seasoned craftsperson can attest that there’s something profoundly satisfying about transforming a vision into a tactile reality.
Step | Action | Purpose | Tips |
---|---|---|---|
1 | Mixing | To prevent a tacky finish and ensure proper cure | Mix for 3-5 minutes, scraping sides and bottom |
2 | Pouring | To distribute resin evenly | Pour slowly and closely to the surface |
3 | Spreading | To cover entire work area | Push resin to edges; don’t stretch it thin |
4 | Torching | To remove air bubbles | Quickly pass torch over; don’t linger in one spot |
5 | Curing | To achieve a hard, durable finish | Leave undisturbed in a dust-free environment |
Remember, each step is as important as the next when you’re working with epoxy. From the blend to the final bubble-popping flick of a torch, all contribute to the immaculate clarity and gleam of your finished piece. In our pursuit of sharing the joys of DIY resin projects, we reiterate: take your time, be thorough, and your resin work will not just sparkle—it will shine unforgettably.
Mastering the Pour: Tips and Tricks
When we talk about crafting with epoxy, the quest for the perfect resin pour is akin to an artist’s pursuit of a masterpiece. The finesse in pouring epoxy resin lies not just in the act itself, but in the thoughtful preparation and application of resin pour techniques. Achieving a flawless finish is about much more than a steady hand; it’s about understanding the medium and respecting the process.
- Begin by mixing your resin thoroughly for at least three minutes. Ensuring that the resin and hardener are completely blended is crucial for avoiding a tacky or incomplete cure.
- Prioritize a clean and level workspace. Any dust or unevenness can ruin the smooth glass-like finish we all strive for in a resin project.
Pouring slowly and steadily is the heartbeat of the process. It prevents the introduction of unwanted air bubbles and allows for superior control, ensuring an even coat across your surface. But remember, be cautious of pouring the last bits from your mixing pot; these may not be as well-mixed and could lead to an imperfect section in your project.
Furthermore, if you desire depth in your craft, consider pouring in layers. This not only adds dimensionality but also gives you room to expel any air bubbles before adding the next layer – a little patience here can lead to a stunning, bubble-free result. Here’s a helpful breakdown:
Layer | Purpose | Technique |
---|---|---|
Base Layer | To provide a foundational surface | Pour and spread evenly, allowing to settle |
Intermediate Layers | To add depth or embed objects | Pour over previous layer, ensuring bubbles are removed |
Top Layer | To seal and finish the piece | Apply carefully to prevent overworking and introducing imperfections |
Patience and precision guide us in this craft. By following these key steps in your resin pouring journey, the rewards are as clear and formidable as the resin itself—breathtaking works of art that withstand the test of time.
Advanced Techniques for Expert Resin Artists
Embracing advanced techniques in expert resin pouring unlocks new dimensions of artistic expression and craftsmanship. At the heart of resin artistry, you will find the seamless blend of precision and creativity, where every tool and technique serves as a conduit for innovation. As we explore these methods, let’s consider how they can enhance the complexity and beauty of our work.
For starters, the integration of pigmented acrylics and enamel paints offers a palette that transforms traditional resin work into an intricate dance of colors and textures. When combined with expert-level artistic epoxy techniques, the results are not only captivating but also profoundly unique to each creator.
Thermal tools, particularly heat guns, are indispensable for an expert resin artist. The careful application of heat allows us to blend colors seamlessly, manipulate the resin’s flow, and, most importantly, evict unwanted air bubbles – all contributing to a work’s aesthetic and structural integrity.
Yet, the true spectacle lies in the layers. Meticulous and thoughtful layering, coupled with the timely introduction of additives, induces depth and a sense of wonder that can make resin pieces appear almost otherworldly.
“To master the art of resin, one must learn not just to see the surface but to also appreciate the depth beneath it.”
- Experiment with new mediums for diverse effects
- Utilize heat to refine and perfect the artwork
- Layer materials strategically for depth
Technique | Materials | Impact on Artwork |
---|---|---|
Color Integration | Acrylics, Enamels | Adds vibrant hues and textures |
Heat Application | Heat Guns, Torches | Enhances blending, removes bubbles |
Layering | Resin, Additives | Builds depth and complexity |
Let these advanced practices in expert resin pouring and artistic epoxy techniques guide us in crafting pieces that resonate with depth, clarity, and a personal touch. The journey from basic pours to profound resin artistry is one of continual learning and passion.
Navigating Bubbles and Other Common Challenges
As we delve into the intricacies of epoxy resin crafting, one of the recurring hurdles we face is the conundrum of removing air bubbles to achieve that smooth resin finish. While bubbles can emerge as an aesthetic feature in certain designs, ensuring their absence is critical when a flawless surface is desired. Let’s explore some effective strategies to keep these resin challenges solved, ensuring our projects exemplify perfection.
Preventing and Addressing Air Bubbles
Addressing the issue of air bubbles starts well before the curing process. Clever mixing and pouring techniques are our first line of defense. By mixing resin and hardener methodically, and avoiding vigorous stirring that can introduce excess air, bubbles are less likely to form. Moreover, pouring in stages can dramatically limit bubble formation. After the pour, a strategic pass with a heat gun or torch encourages any trapped air to rise to the surface and escape, resulting in a smoother finish.
Strategies for a Smooth Finish
To enhance our tactical approach further, we’ve compiled an effective set of strategies for achieving a smooth resin surface every time. Consider the following comparative table to articulate the paths for managing various challenges:
Challenge | Strategy | Expected Outcome |
---|---|---|
Air Bubbles on Surface | Use a heat gun/torch after pouring | Bubbles pop, leaving a smooth surface |
Incorporating Bubbles as Design | Controlled stirring and partial curing | Intentional bubbles stay trapped as artistic elements |
Thick Pour Bubble Issues | Multiple thin layers instead of a thick pour | Reduced bubble formation and easier management |
Dome Edges on Pieces | Guide and limit resin flow to edges | Smooth, neat edges with a professional finish |
By applying these approaches, not only do we remove air bubbles, but we also navigate the myriad of challenges presented when working with resin. The goal is not just to solve problems but to implement proactive measures that enhance our craft. Each project becomes an opportunity to refine our technique and testify to the beauty of flawlessly cured resin.
Mastering Layers: The Key to Depth and Clarity
In our commitment to crafting visually stunning resin art, resin layering stands out as our definitive technique for introducing breathtaking depth and unmatched clarity into each piece. Layer by layer, we build not only a physical form but also weave the narrative of our collective capability to create.
When dealing with resin depth techniques, timing is crucial. From our experience, allowing each layer to reach a point of partial curing sets the stage for the next pour, ensuring a synergy between strength and beauty. Moreover, this approach practically eliminates the concern of undue merging colours or details from different layers.
With deep pour resin, we can delve into more formidable projects, constructing layers of up to two inches thick without the worry of incomplete curing or unsightly blemishes. This generous depth allowance opens the door to more dynamic art pieces, where elements can be embedded with distinct features, and shadows can dance with light.
- Prepare your work surface ensuring it is clean, dust-free, and level.
- Mix the deep pour resin according to manufacturer’s instructions for optimal consistency.
- Apply the first layer, using a heating tool to gently coax air bubbles to the surface and away.
- Monitor curing, and when tacky to the touch, pour the succeeding layer, repeating the bubble removal process.
- Continue layering, taking care not to rush the process, for complex multi-dimensional pieces.
Our expertise demonstrates that the clarity of resin is not solely in its transparent nature but significantly in our precision of layering. By steadfastly adhering to these steps, we transform the functional into formidable, melding art with technique for a truly awe-inspiring result.
Exploring Creative Applications of Resin Pouring
When we delve into the world of resin creative applications, we uncover more than just a crafting trend; we tap into a platform where imagination meets tangible expression. Resin art allows for an awe-inspiring range of color and form. From vibrant, chromatic displays to the subtle interplay of light and shadow, each piece champions its own fingerprint of creativity.
Incorporating Colors and Additives for Stunning Effects
By introducing color additives in resin, the ordinary becomes extraordinary. Pigments can shift from translucent whispers to bold statements, while spray paints bring swift, airy dynamism. The addition of glitters and reflective metals can transform a simple pour into a shimmering tableau, catching every glance with a new angle of light.
Resin Art and Functional Pieces – Bridging Creativity and Utility
Functional resin art not only captivates aesthetically but also serves pragmatic purposes. A resin-coated table isn’t just a statement piece in a living room; it’s also a durable, everyday surface that resists wear and tear. In the same vein, resin-cast jewelry encases delicate natural elements in wearable forms, protecting their beauty while endowing the wearer with a unique piece of adornment.
Resin Additive | Visual Effect | Functional Application |
---|---|---|
Pigments | Depth of Color | Art Pieces, Tabletops |
Spray Paints | Airy, Effervescent Layers | Wall Decor, Functional Art |
Glitters/Metals | Reflective and Textured Finish | Jewelry, Home Accessories |
Broken Crystals/Gold Pigments | Dimensional Texture | Statement Artworks, Furniture Inlays |
As we experiment with these variables, we create not just art but personal experiences—our resin projects behold stories, encapsulate moments, and infuse environments with a piece of our essence. Each new project unfolds an opportunity to challenge the ordinary, to craft something not only beautiful to behold but invaluable in its utility.
Safety First: Navigating the Hazards of Resin Use
When it comes to creating with resin, emphasizing resin safety is not a matter we take lightly. The malleable medium is celebrated for its versatility, but it’s our duty to be well-informed about the potential epoxy resin hazards it poses. Ensuring the well-being of ourselves and those around us is just as important as achieving the perfect glossy finish. As we guide you through the best practices for handling resin, it is our aim to equip you with the knowledge of protective measures resin enthusiasts should adopt for a secure crafting journey.
Proper Ventilation and Protective Gear
Working with resin requires mindfulness about the workspace environment. The first line of defense in ensuring a safe crafting experience is setting up in a well-ventilated area. This could mean working near an open window or using an exhaust fan to keep the air circulating and to prevent the accumulation of hazardous fumes. But ventilation is just the beginning; dress for the job with the appropriate protective gear. Gloves, long-sleeved shirts, safety goggles, and respirators must become part of your standard equipment to shield your skin and lungs from exposure to resin and its vapors.
Handling and Disposal of Resin and Supplies
Resin’s sticky nature requires diligent care when handling. Always use designated tools and containers, and avoid direct skin contact whenever possible. In terms of disposal, the goal is to minimize environmental impact. Follow the manufacturer’s guidelines to dispose of resin correctly. This often involves curing any unused resin before disposal to prevent harmful chemicals from leaching out.
Protective Measure | Reason | Best Practice |
---|---|---|
Gloves | Avoid skin irritation | Wear nitrile or latex gloves |
Respirator | Inhalation of toxic fumes | Use a respirator with organic vapor cartridges |
Safety Goggles | Prevent eye contact | Wear goggles that form a protective seal |
Ventilated Area | Reduce inhalation risk | Work near an open window or use an exhaust fan |
Proper Disposal | Environmental protection | Cure unused resin; follow local disposal regulations |
Taking these proactive steps will not only enhance your resin experience but also promote a healthier environment for all. Indeed, we must be as meticulous with our safety protocols as we are with our artistic endeavors. A well-prepared artist is not only a skilled one but a responsible member of the resin crafting community.
Troubleshooting: Solving Common Pouring Pitfalls
When embarking on resin projects, encountering stumbling blocks like sticky or uncured resin, or unpredictable reactions is part and parcel of the experience. Fortunately, with a bit of know-how in resin troubleshooting, these challenges can quickly become a thing of the past. Here, we’ll delve into practical uncured resin solutions and strategies for fixing resin issues that are all too common in the crafting realm.
Dealing with Sticky or Uncured Resin
Sticky resin is a clear sign that something has gone awry during the mixing or curing phase. It often boils down to misjudged ratios or inadequate mixing. By taking extra care with measuring and mixing, you can overcome this issue. If you find that your project has a sticky surface even after the advised curing time, here are a few steps you can try:
- Check your resin-to-hardener ratio once more to ensure accuracy.
- If necessary, pour a fresh layer of correctly mixed resin over the sticky spots.
- Utilize mild heat to assist in the curing process, but do so with caution to avoid any unwanted reactions.
Fixing Uneven Surfaces and Unexpected Reactions
Uneven surfaces can be the bane of any resin artist’s existence, but this can often be rectified with a level work surface and a keen eye for detail. Should unexpected reactions occur, such as cloudiness or color shifts, consider the compatibility of any added materials or the environmental conditions at play. Here’s what you can do to smooth things out:
- Before you begin your pour, ensure the working surface is perfectly level.
- After pouring, gently guide the resin to the edges and avoid overworking it.
- Investigate any additives you’re using to ensure they’re fully compatible with the resin.
Understanding the root causes of common resin issues is essential for perfecting the craft. As challenging as these issues may be, they serve as valuable lessons that bolster our skill set. Remember, persistence and patience are your allies in achieving that impeccable resin finish you’re after.
Conclusion
In the grand tapestry of resin craftsmanship, mastering resin pouring is not merely about mixing and settling – it is an embrace of artistic expression blended with precision. As we’ve explored the vast world of creative resin projects, it’s become clear that success in this medium is measured by clarity, shine, and the seamless merger of colour and form. The meticulous nature of epoxy resin demands patience, a steady hand, and an informed approach to each project, yet the satisfaction derived from a successful resin art piece is undeniably profound.
We’ve journeyed together, from our first tentative pour to the confident creation of intricate and dazzling works of art that embody our shared aspirations. It is in the details that the true challenge lies – balancing safety with innovation, and technique with the unpredictable whims of creativity. Our shared experiences speak to the commitment required to excel in this craft, reminding us that working with resin is as much about the process as it is about the result.
As we continue to cultivate our skills and broaden our horizons, we remain captivated by the limitless possibilities that epoxy resin provides. It’s an honor to share our stories, be they about navigating the trials of running a business, living with osteoporosis, or supporting loved ones with mental disabilities. Each experience enriches us and lends authenticity to our creations. Through resilience and passion, the beauty of resin art continues to thrive in our community, a reminder of our collective quest towards mastery and the sheer joy found in each new, glistening piece.
FAQ
What is the best pouring technique to avoid imperfections in resin?
The best pouring technique involves pouring the resin slowly and as close to the surface as possible to minimize air entrapment. Use a controlled hand to maintain a steady flow and spread the resin evenly across the surface, and remember to torch out bubbles shortly after pouring.
How do I prevent air bubbles in my resin art?
To prevent air bubbles, ensure you mix resin and hardener properly, pour in thin layers rather than a single thick one, use a heat source like a heat gun or torch to pop surface bubbles, and avoid whipping air into the mixture during stirring.
What are the consequences of a clumsy pour when working with epoxy resin?
A clumsy pour can result in a variety of imperfections such as air bubbles, divots in the surface, uneven finishes, and ‘icicles’ or drips around the edges. To avoid these, use a slow and controlled pouring technique and level your working surface beforehand.
How do I choose the right epoxy resin for my project?
Selecting the right epoxy resin depends on the type of project you’re working on. Consider using casting resin for intricate jewelry, tabletop epoxy for surfaces like counters or bars, and deep pour epoxy for thicker pieces. Always read manufacturer guidelines for the best results.
Can I pour resin in layers for my project? How thick can each layer be?
Yes, pouring resin in layers is often recommended, especially for deeper projects. For standard tabletop epoxy, aim for a self-leveling thickness of about 1/8 inch per layer. For deep pour resin, you can typically create layers up to two inches thick if the product allows for it, but always verify the manufacturer’s recommendations.
What are some advanced techniques for creating unique resin art?
Some advanced techniques for resin art include the use of different colorants, like pigmented acrylics or metallic powders, layering with various translucent and opaque mediums, and the strategic use of thermal tools to manipulate the resin and eliminate bubbles.
How do I ensure my resin pour has a professional, flawless finish?
To ensure a professional finish, work in a dust-free environment, pour resin slowly and evenly, use adequate lighting to spot any bubbles, and apply heat to remove them. Additionally, allow each layer to partially cure before adding the next, if layering is a part of your technique.
What safety precautions should I take when working with resin?
When working with resin, always do so in a well-ventilated area, wear protective gloves and a mask to avoid contact with skin and inhalation of fumes, and follow safety guidelines for handling and disposing of resin materials.
How can I fix sticky or uncured resin?
Sticky or uncured resin can often be fixed by pouring a fresh layer of properly mixed resin on top. Ensure your working environment is at the correct temperature and the resin-to-hardener ratio is accurate. Always mix thoroughly for the time specified by the manufacturer.
How can I troubleshoot unexpected reactions or fix uneven surfaces in my resin art?
For uneven surfaces, make sure your work area is level before you begin pouring. If you encounter unexpected reactions, review the compatibility of any additives you’ve used with your resin. Consider conducting a small test pour when working with new materials or combinations.
What are some creative applications of resin pouring?
Creative applications of resin pouring include making jewelry, art canvases, furniture, coasters, and more. By incorporating additives such as pigments, glitters, or objects such as flowers and beads, you can create unique textures and finishes that enhance the aesthetic of your pieces.
How do I add color and special effects to my resin projects?
To add color and special effects to resin projects, you can use a range of additives like liquid dyes, powdered pigments, glitters, and small objects. These can be mixed into the resin before pouring or added between layers to achieve different visual outcomes and textures.
Source Links
RELATED POSTS
View all