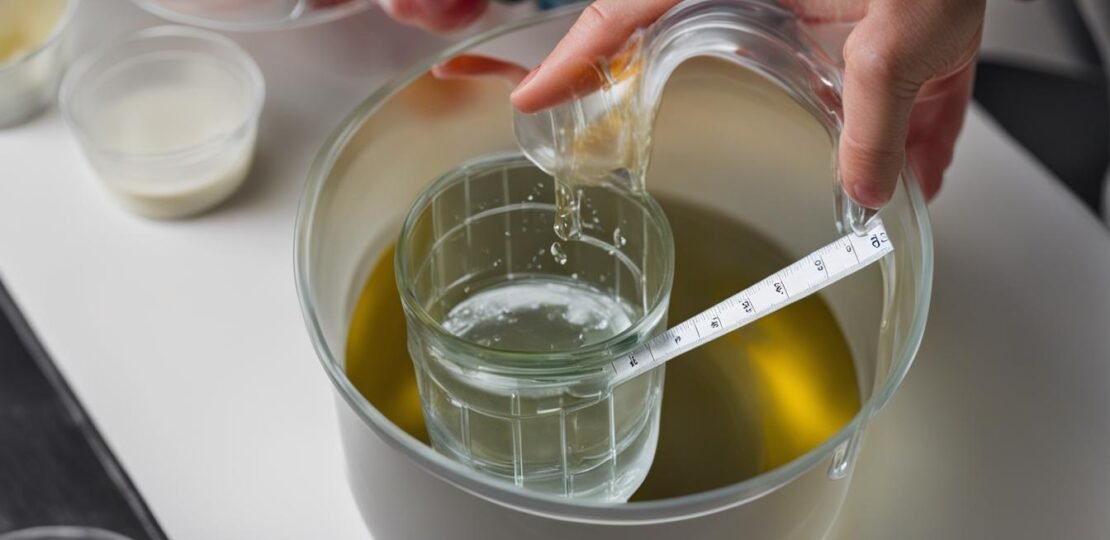
In the shared studio space where artistic fervor pulses through the air, we confront our personal dragons each day. My husband grapples with the shadows of mental illness—agoraphobia, anxiety, and depression—while my journey is marked by the brittle nature of bones, a condition known as osteoporosis. Within these walls, our struggles have taught us the art of resilience, reinforcing our spirits even as our bodies demand care.
Our art has proven to be more than a passion; it’s become a soothing balm, a medium through which we transform our battles into a beacon of hope and color. This art, especially our mutual endeavor in resin projects, requires not just creativity but precision—measuring resin accurately is as important as the brushstroke on canvas. The quest for the perfect epoxy mixture parallels our personal quests, each measurement a step towards the oasis of peace we’ve cultivated.
As we pour and mix, stirring steadily, each step in how to measure resin is done with care, mirroring the attentiveness we provide to each other. Through our website at www.devilndove.com, we invite you to witness the alchemy of love, resilience, and precision that defines every facet of our shared existence.
Essential Insights
- The precision of blending resin and hardener is a metaphor for our balanced partnership in life and art.
- Challenges in mental health and physical well-being can be faced with creativity and mutual support.
- Artistic ventures offer a haven for expression and refuge amid life’s tumult.
- Mastering the technicalities of resin work symbolizes our commitment to quality and detail.
- Resin art fosters a unique form of resilience that is both tangible and spiritual.
- Community and support play a central role in navigating the complexities of health and craftsmanship.
Understanding the Basics of Epoxy Resin
Welcome to an exploration of the foundational elements behind one of the most versatile materials in the crafting and industrial worlds: the epoxy resin system. In our collective journey, we recognize the importance of precision and knowledge in the curing process, as well as delving into the fascinating chemical reaction that transforms liquid into an impressively epoxy solid.
Let’s delineate the fundamental principles. At its most basic level, any epoxy resin system consists of two components: Part A, the resin, and Part B, the hardener. When these two elements are combined in correctly measured proportions, a chemical reaction is initiated. This is the moment of transformation—an intricate dance of molecules that will determine the integrity and strength of the final product. It’s an alchemical process we hold in high regard, for it requires not just raw materials but an intimate understanding of their nature.
The key to success with epoxy resin is twofold: selecting the right system, such as Super SAP CLR epoxy from Entropy Resins, and executing the precise mix ratios as advised by the manufacturer. This is not merely a recommendation but a crucial step to ensuring the anticipated durability and appearance of any given epoxy project. Our commitment is to ensure these ratios are respected diligently, fostering the desired outcome—a solid epoxy of the highest quality.
Epoxy Resin System | Curing Agent (Part B) | Mix Ratio by Volume | Mix Ratio by Weight | Typical Cure Time |
---|---|---|---|---|
Super SAP CLR Epoxy | CLR Hardener | 2:1 | 100:45 | 12-24 hours |
Super SAP CCR Epoxy | CCR Hardener | 2:1 | 100:43 | 6-10 hours |
Super SAP BRT Epoxy | BRT Hardener | 3:1 | 100:33 | 8-16 hours |
In this journey, we empower and support one another, acknowledging the challenges we face, both personally and professionally, from running a business with Osteoporosis to caring for a partner with mental disabilities—a testament to our resilience and dedication.
We invite you to reflect on the beauty of chemistry that resides within the crafting of epoxy. Together, we delve into the realms of creation and innovation, where a well-orchestrated curing process ensures our materials transform from viscous potential to robust reality. There’s a certain magic here—a clear vision cast and solidified into tangible form. And so, we continue to share, learn, and thrive within this intricate dance of elements.
Key Equipment for Accurate Resin Measurement
When it comes to resin art and projects, precision is key—especially in measuring your materials. The first step in achieving this accuracy begins with assembling the appropriate tools and safety equipment. Only with these can we ensure that our projects meet the highest standards while maintaining a safe environment for us to work in. Below, we delve into the essential gear and instruments vital for the precise measurement of resin, an integral part of the resin crafting process.
Protective Gear for Safe Handling
Our health and safety are paramount when working with resin. Therefore, we never skimp on eye protection to shield our eyes from splashes, and we always wear disposable gloves to prevent skin contact with the epoxy, which can cause irritation. These gloves should be replaced regularly throughout the process to maintain cleanliness and prevent contamination of the resin mixture.
Choosing the Right Containers and Tools
For that precision we keep mentioning, it’s essential to use a digital scale known for its sensitivity to small weight differences. We also lean on graduated cylinders for accuracy when measuring by volume, as their clear markings make it easy to achieve exact measurements. And let’s not forget about clean mixing sticks—indispensable for a bubble-free and consistent mix.
Choosing the right containers for the mix is just as important; we look for materials that won’t react with the resin itself. While glass or foam containers are a no-go, those made of plastic, metal, or wax-free paper are our go-to options, ensuring the integrity of the resin isn’t compromised.
https://www.youtube.com/watch?v=xRp8uoSNPzQ
Item | Description | Purpose |
---|---|---|
Eye Protection | Safety goggles or glasses | To shield eyes from harmful splashes |
Disposable Gloves | Latex or nitrile gloves | To protect skin from epoxy resin |
Digital Scale | High precision scale | For accurate weight measurements |
Graduated Cylinders | Marked measurement containers | For precise volume measurements |
Mixing Sticks | Clean, smooth sticks | To mix resin and hardener thoroughly |
In the end, the success of our resin projects comes down to meticulous attention to detail—and that begins with having the right equipment. By prioritizing safety and precision, we lay the foundation for outstanding results in our artistic endeavours. From the digital scale to graduated cylinders, each item plays its part in ensuring our measurements are spot on, so our creativity can flourish uninhibited.
Resin Selection: Types and Brands
When it comes to selecting the right resin for your project, the type and brand of resin can be the difference between success and a sticky situation. Among the myriad choices available, Entropy Resins, particularly their Super SAP CLR, stands out as a reliable option for those seeking quality results. This two-part epoxy system offers a perfect balance of strength and clarity when mixed and cured according to specifications.
We understand that engaging in a meticulous resin selection process is crucial. As artisans and business owners who navigate the challenges of managing our enterprise with personal commitments including a mentally disabled partner, we know that choosing dependable materials is a non-negotiable aspect of maintaining professional standards. Below you’ll find a comparative view elucidating the particular properties and applications of various two-part epoxy systems that you might consider for your creative ventures.
Epoxy System | Mix Ratio (Resin:Hardener) | Viscosity | Primary Use Cases |
---|---|---|---|
Super SAP CLR | 2:1 by volume | Low to Medium | Jewelry, Surfboard Coating, Clear Casting |
Brand B Epoxy | 1:1 by weight | Medium | Tabletops, Artwork, Laminating Wood |
Brand C Resin | 3:1 by volume | Medium to High | Mould Making, Industrial Applications |
Keeping in mind that every epoxy brand has its distinct properties, it’s essential to refer to the manufacturer’s specifications for the exact mix ratio and additional instructions. Properly adhering to these details ensures that the resin system you’ve selected is suited to your application, thus delivering a finish that is both clear and strong.
With insights like these, we’re confident you can make an informed resin selection that not only meets the demands of your craft but also supports the diligent workflow required when running a business against the backdrop of personal care responsibilities.
Measuring Resin by Weight Versus Volume
When embarking on a project that involves epoxy resin, achieving the desired result hinges on the accuracy of your measurements. Whether you’re using this versatile substance for professional applications or artistic creations, comprehending the subtleties of measuring by weight versus volume will guide you to success. Let’s delve into why precision and correct volume accuracy are crucial in handling epoxy resin.
Using a Digital Scale for Precision
To ensure that every component of your resin mixture is properly balanced, employing a digital scale is indispensable. Digital scales boast precision that’s essential when you measure epoxy resin, allowing you to weigh each part of the mixture with an accuracy down to 0.01 ounce or gram. By leveraging the tare feature, you can effortlessly calculate the net weight and adhere to the mix ratio with fidelity. This method is unfailingly precise, making it a preferred choice for projects where the stakes are high.
Understanding Graduated Mixing Cups for Volume Accuracy
Conversely, graduated mixing cups offer a different approach, perfect for those who measure in terms of volume. These cups are marked with clear graduations, enabling you to pour the resin and hardener with volume accuracy. Observing the meniscus of the liquids meet the calibrated lines ensures that you achieve the correct ratio as stipulated by the resin manufacturer. While this method may be preferred for its simplicity, it still requires a keen eye and a steady hand to ensure that each measurement is accurate.
We understand that choosing between weight and volume measurement can be as much about personal preference as it is about the specifics of the project at hand. Using both a digital scale for its unrivaled precision and graduated mixing cups for their straightforwardness will provide you with flexibility and the ability to adapt to varying circumstances. Mastering these tools will ultimately refine your work and elevate the caliber of your final product.
Mixing Ratios and Their Importance in Resin Work
As we explore the intricate world of epoxy creations, we come to understand that the mix ratio is more than just a set of numbers—it is the essence of achieving a successful curing of resin. Attaining the correct chemical balance between resin and hardener is not merely a recommendation; it is a non-negotiable standard for professional results.
Let us delve into the precision that resin work demands. Each manufacturer’s instructions act as a sacred scripture for the epoxy enthusiast. To circumvent the risks of a compromised final product—a too flexible or brittle creation, or worse, an exothermic misadventure—scrupulous adherence to the prescribed mix ratios is paramount.
Remember, the journey from liquid to solid is a path defined by chemical laws, where each step is measured and each ingredient accounts for the strength and clarity of the end product.
In the table below, we see a side-by-side comparison, illustrating how deviations from the mix ratio can lead to various curing issues that compromise the structural integrity and aesthetics of a resin project.
Mix Ratio Deviation | Potential Curing Issue | Resulting Problem |
---|---|---|
Too Much Hardener | Accelerated Curing | Increased Risk of Cracking or Yellowing |
Too Much Resin | Soft, Tacky Finish | Weak Structural Integrity |
Incorrect Proportioning | Incomplete Curing | Lack of Clarity and Overall Quality Deterioration |
In our collective experience, we find that whether through the use of reliable pumps or by trusty hand measurement, the goal remains the same: to ensure that each mixture manifests into a hardened version of our envisioned design, flawless and precise.
We invite fellow artisans to join us in the pursuit of resin perfection. With every carefully balanced mixture, we lay the foundation for a masterpiece that not only stands the test of time but also showcases the beauty of meticulous craftsmanship.
Practical Guide to Mixing Resin and Hardener
Once we’ve measured our resin and hardener accurately, the next crucial step is the mixing process. This is where achieving the perfect epoxy consistency comes into play, essential for the success of any project. Mixing resin isn’t just about combining two substances; it’s an art that requires patience and technique to avoid common mixing mistakes.
Stirring Techniques for a Consistent Mixture
Mixing resin and hardener together effectively is essential for ensuring a uniform consistency without any streaks. It’s not just a simple stir; it’s about integrating both components thoroughly. We recommend stirring for no less than 2 to 3 minutes, making sure to regularly scrape the sides, corners, and bottom of your mixing container. This method ensures that every bit of the mixture achieves the same homogeneity and cures correctly.
A pro tip: Stir slowly to minimize air bubbles, which can affect the clarity and quality of your final cured resin.
Common Mixing Mistakes to Avoid
When mixing resin, there are a few pitfalls that you need to be mindful of. Insufficient stirring time is a primary culprit that can result in a tacky or unevenly cured final product. Confidence in stirring techniques and a watchful eye on the epoxy consistency can skirt most of these issues.
- Avoid rushing the process; patience is key.
- Do not pour unmixed resin from the sides into your project, which could lead to uncured spots.
- Ensure that no part of the mixture is left unstirred; thoroughness is non-negotiable.
Let’s take a closer look at the vital steps and possible missteps in a table format.
Step | Key Focus | Common Mistakes |
---|---|---|
Preparation | Gather all necessary equipment | Using reactive containers or incorrect ratios |
Stirring | Uniform consistency, 2-3 min stirring | Insufficient stirring, ignoring container edges |
Pouring | Gentle pour to avoid air bubbles | Pouring too quickly or incorporating unmixed residue |
In conclusion, by mastering these stirring techniques and avoiding the common mixing mistakes, we help ensure that our resin projects come out flawless every time. A well-mixed resin is the foundation of a successful project, bringing our artistic visions to life with strength and clarity.
Advanced Tips on Dispensing Prepared Resin
When we’ve meticulously mixed our epoxy resin, mastering the art of dispensing epoxy resin becomes the next crucial step. It’s not just about pouring and hoping for the best; we consider a variety of environmental factors and employ specific layering techniques to ensure a flawless resin application. Before we delve into the nuances of these applications, it’s essential to understand the role of our surroundings. Temperature and humidity can be our allies or foes in the world of resin work.
Environmental Factors Affecting Epoxy Application
First and foremost, successful resin projects hinge on recognizing and adjusting to the environment. We aim for conditions that allow our resin to cure slowly and evenly. This is why we carefully monitor our workshop’s temperature and humidity levels, steering clear of extreme conditions that might affect the curing process.
Layering Techniques for Optimal Results
Next, we put our attention to layering techniques. Starting with a thin, evenly spread layer, we often use a squeegee, following this with a brush to smooth out any inconsistencies, eliminating air bubbles and preventing waste. Our focus on efficiency and precision in these initial phases pays off in the quality and aesthetics of our final pieces. Here’s a table of our curated tips for ideal resin layering:
Step | Action | Goal |
---|---|---|
1 | Apply first layer with squeegee | Establish a thin, even base |
2 | Smooth with brush | Eliminate air pockets and ensure even coverage |
3 | Allow to tack before next layer | Enable proper adhesion for subsequent layers |
4 | Apply additional layers as needed | Achieve desired thickness and finish |
Adhering to these steps when dispensing epoxy resin, we navigate through the project with confidence. By allowing each layer to attain the right level of tackiness, we’re ensuring strong bonds and a seamless finish. This attention to detail and process yields creations that are not only sturdy and reliable but also visually stunning.
Surface Preparation for Epoxy Adhesion
When it comes to achieving proper adhesion for your epoxy projects, the surface preparation is a step we can’t afford to overlook. It’s the unsung hero of creating enduring secondary and chemical bonding for your crafts or repairs. Let’s examine the essential steps we must adhere to for successful results.
To start, we focus on the cleanliness of the surface, which is the foundation for a robust mechanical bond. Any contaminants such as dust, oils, or grease are adversaries of adhesion and must be thoroughly removed. For those aiming for a primary bond or chemical attachment, remember, timing is everything. Applying fresh epoxy over partially cured surfaces creates a chemical connection that’s both strong and reliant on the careful timing of application.
Here’s a tip: Improperly prepared surfaces could lead to a weak bond and potential failure of the project. For this reason, sanding may be necessary to create the desired texture, particularly when dealing with fully cured epoxy. This not only aids in surface preparation but also maximizes the potential of subsequent layers for a flawless finish.
- Mechanical Bonding: Ensure the surface is clean and textured for the epoxy to “key into.”
- Chemical Bonding: Apply a fresh layer of epoxy over a partially cured base to create a seamless bond.
- Release Agents: Utilize materials like PVA or clear plastic films to prevent unwanted bonding to moulds or workspaces.
To further elaborate on the importance of the process, let’s explore the differences between the two types of bonds we’re aiming for:
Mechanical Bond | Chemical Bond |
---|---|
Clean and texturize surface for epoxy to mechanically interlock | Applying fresh epoxy to partially cured epoxy for a chemical connection |
Lastly, for scenarios where we wish to prevent the epoxy from bonding onto unnecessary areas, the use of release agents is critical. Strategically applying these agents will allow us to maintain control over where our epoxy sets, ensuring a neat, professional outcome. By diligently following these guidelines, the proper adhesion of your epoxy work will certainly stand the test of time.
Ensuring Proper Cure: Techniques and Troubleshooting
When it comes to curing epoxy resin, the process is about precision and patience. To ensure that your resin project is successful, spotting potential issues early can save a lot of time and materials. One common issue in the curing process is Amine Blush, which can affect adhesion and the cosmetic finish. Additionally, troubleshooting sticky resin can be a challenge when the expected hard, polished results aren’t met. By mastering these tactics, we can guarantee an optimal cure every time.
Identifying and Preventing Amine Blush
Amine Blush is a tricky condition where a waxy layer forms on the surface during the curing phase, primarily due to moisture. This blush can hinder subsequent layers from bonding properly and dull the shine of your finish. The table below showcases some proactive steps you can take to prevent Amine Blush:
Preventative Measures | Reason |
---|---|
Environment control | Ensuring that the workspace is at an optimal temperature and humidity level reduces the chances of blush forming. |
Resin quality | Using high-quality resins, which are less prone to blushing, can help mitigate the problem. |
Protective cover | Covering your project while it cures can shield it from airborne moisture. |
Handling Uncured or Sticky Resin
If you discover that part of your resin has not cured and is rather sticky, don’t panic. Here are a few troubleshooting sticky resin steps we find helpful:
- Determine if the mix ratio of resin to hardener was correct.
- Check if the resin and hardener were adequately mixed together.
- Adjust the curing environment, ensuring it’s warm enough for the resin to cure.
Remember, patience is key. It might be tempting to rush and fix the issue, but understanding the root cause will lead to the best corrective action. And of course, sometimes it might just be a matter of giving it more time to reach the full cure. Stay vigilant and maintain a thorough checklist; this will help ensure that your epoxy projects always turn out as expected.
Conclusion
As we’ve explored, successful resin measuring is a cornerstone to crafting with epoxy. This diligent practice ensures that each of our creations comes to life in the envisioned perfection. Our journey into the world of resin has taught us the value of precision—a lesson we apply diligently as we navigate the intricacies of running our business amidst personal challenges. From ensuring a perfect epoxy mixture to the intricacy of the resin curing process, every step is executed with utmost care.
We understand the importance of mastering resin techniques to produce pieces that are as strong and clear as our resolve in the face of life’s tests. Hand-in-hand, we tackle the technical details, mix ratios, and environmental factors to bring forth artistry that stands as a testament to our resilience. It’s not just about what we create, but the passion and precision we infuse into every piece. The art of working with resin mirrors the complexities and care we invest in our personal lives; each day, we pour our hearts into both, striving for excellence.
In embracing our creativity, we’ve also embraced a community that supports one another through life’s challenges. Our experiences—be it in meticulously executing a new resin project or supporting each other through health and personal matters—remind us that the most enduring masterpieces are crafted with love and tenacity. As we continue to perfect our craft, we invite you to support our journey and witness the endless possibilities that come with a meticulous approach to resin artistry. Together, we are not just artists; we are a testament to the enduring human spirit.
FAQ
What do I need to know before measuring resin for my project?
Before you begin measuring resin, it’s essential to understand the importance of accuracy for the perfect epoxy mixture. Each resin system has a specified mix ratio that needs to be followed for the resin to cure correctly. The ratio ensures the proper chemical balance, crucial for the epoxy to turn into a solid and durable material.
How do I ensure safety while handling epoxy resin?
Safety should always be your top priority. Protective gear, including eye protection like safety goggles and disposable gloves, will protect your skin from possible irritation and your eyes from splashes. It’s also important to work in a well-ventilated area to limit exposure to fumes.
Can I use any container for mixing epoxy resin?
No, you should be selective about the containers you use to mix epoxy resin. Avoid containers made of materials that can react with the epoxy, such as glass or foam. Safe materials include plastic, stainless steel, or wax-free paper mixing cups. Remember that your tools, like mixing sticks, should also be clean to prevent contamination of the resin.
Why does it matter which epoxy resin product I choose?
Different epoxy resin products, such as Entropy Resins’ Super SAP CLR, come with varying properties and mix ratios. Selecting the right type and brand is essential for your project’s success as they ensure the final product’s clarity, strength, and curing time meet your expectations.
Should I measure epoxy resin by weight or volume?
The method of measurement depends on the specific requirements of the resin system you’re using. Measuring by weight using a digital scale is precise to 0.01 ounces or grams and is ideal for most two-part epoxy systems. When measuring by volume, graduated mixing cups offer an accurate ratio based on the manufacturer’s instructions.
Why is the mix ratio so crucial in resin work?
The mix ratio of resin to hardener dictates the chemical reaction necessary for the epoxy to cure properly. Follow the manufacturer’s specifications exactly, as an incorrect ratio can lead to issues like uncured or weak end products, or in some cases, an accelerated and potentially hazardous reaction.
What is the best technique for mixing resin and hardener?
A consistent mixture is achieved by stirring the resin and hardener together thoroughly for at least 2 to 3 minutes. Pay special attention to the sides and bottom of the container. Poor mixing can result in a mixture that doesn’t cure correctly, leading to a compromised final product.
What should I watch out for when dispensing prepared resin?
Factors like temperature and humidity can greatly affect how epoxy cures. It’s best to avoid dispensing resin on cold or humid days. Use techniques like spreading a thin layer with a squeegee and then smoothing with a brush to ensure even coverage and prevent wasting any material.
How important is surface preparation for successful resin adhesion?
Surface preparation is crucial. Mechanical bonds require cleanliness and texture for the resin to adhere properly, whereas primary bonds require chemical bonding by applying fresh epoxy over partially cured epoxy. When you’re aiming for additional layers over cured epoxy, sanding and cleaning may be necessary to ensure adhesion.
What is Amine Blush, and how do I handle it?
Amine Blush is a waxy byproduct that can appear on the surface of the epoxy as it cures, often in cool, moist conditions. To prevent inadequate bonding of subsequent layers, it’s crucial to remove any blush by washing the surface with water and an abrasive pad, thus ensuring a clean and ready base for further applications.
What should I do if my resin hasn’t cured properly?
If you encounter uncured or sticky resin, re-evaluate your mix ratio and mixing process. Sometimes environmental adjustments need to be made, such as temperature or humidity control. If the issue persists, carefully examine whether the measurements were precise and if the materials were thoroughly mixed.
How do I master the process of working with epoxy resin?
To master crafting with epoxy resin, you must follow the precise mix ratio of the resin and hardener, use appropriate measuring and mixing techniques, prepare your working surface correctly, and address any curing issues. Practice, patience, and a consistent methodical approach are key to achieving professional-quality results.
Source Links
RELATED POSTS
View all