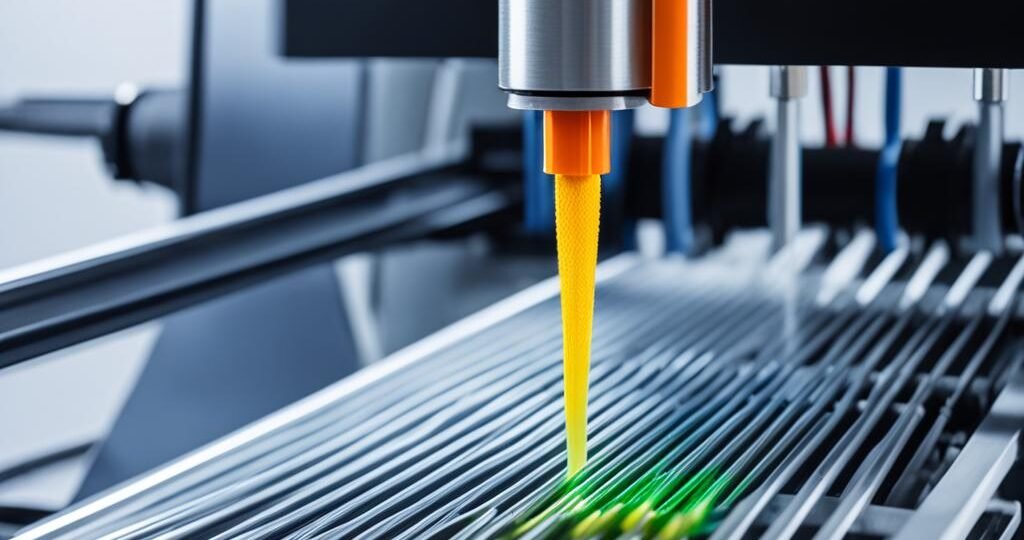
In today’s world of 3D printing, achieving optimal prints requires more than just pressing a button. To truly unlock the potential of this technology, you need to understand how to adjust the layer height settings. Layer height refers to the thickness of each layer that the printer extrudes and it plays a crucial role in the resolution, strength, and appearance of the final print.
Changing the layer height settings may sound daunting, but with a little guidance, you’ll be able to effortlessly fine-tune your prints. The key lies in the slicer software, the program that converts a 3D model into instructions for the 3D printer. This software allows you to customize various parameters, including layer height.
In this tutorial, we will demystify the process of adjusting layer height in 3D printing. We will walk you through the steps, provide tips for optimizing layer height, troubleshoot common issues, and offer best practices for achieving exceptional results.
Key Takeaways:
- Layer height is the thickness of each layer in a 3D print.
- Adjusting layer height settings is crucial for print resolution, strength, and appearance.
- Slicer software allows for customization of layer height.
- Consider factors such as print detail, surface smoothness, filament usage, and printing time when choosing layer height.
- Troubleshoot layer height issues, such as inconsistent layers or layer shifting, by adjusting settings and checking hardware.
Now that we have set the stage, let’s dive into the world of layer height adjustment in 3D printing and unlock the full potential of your prints.
Support us at www.devilndove.com or our store at www.devilndove.online
What is slicer software and how to change layer height settings?
Slicer software plays a vital role in the 3D printing process, transforming a 3D model into specific instructions for the printer. This software allows us to adjust various parameters, including the layer height. The layer height setting directly influences the print quality, determining the thickness of each layer that the printer extrudes.
To change the layer height settings, we need to access the print quality or layer resolution options within the slicer software. Depending on the software you are using, you can choose from preset values or enter a custom value of your own. Preset values are pre-defined options that provide a convenient way to adjust the layer height according to specific requirements or desired outcomes. On the other hand, custom values allow us to fine-tune the layer height based on our preferences, giving us more control over the print quality and precision.
Another important parameter to consider is the initial layer height. The initial layer is typically printed at a slightly higher height compared to the subsequent layers. This intentional height difference helps establish better adhesion to the build plate, minimizing the risk of warping and improving the overall print quality. By adjusting the initial layer height, we can optimize the initial adhesion while maintaining consistent layer heights throughout the rest of the print.
Understanding how to navigate the slicer software and change the layer height settings is crucial for achieving the desired print quality and resolution. With the right adjustments, we can optimize our 3D prints for various applications, ensuring that each layer is printed with precision and accuracy.
An illustration showing how to change layer height settings in slicer software.
Factors to consider when choosing a layer height
When it comes to 3D printing, selecting the right layer height is crucial for achieving the desired print quality and appearance. There are several factors to consider that can impact the final result.
Print Detail and Surface Smoothness
The layer height plays a significant role in capturing fine details and achieving a smooth surface finish. A lower layer height allows for more precise prints, resulting in higher levels of detail and smoother surfaces.
However, it’s important to note that using a lower layer height requires more filament and longer printing times. So, if print detail and surface smoothness are essential for your project, it might be worth the additional time and material usage.
Print Appearance
The choice of layer height also influences the overall appearance of the print. Lower layer heights can make the print look more like the original model, with intricate details accurately represented.
In contrast, higher layer heights may result in prints that resemble a stack of pancakes. Although the print’s overall strength might increase, the resolution decreases, and the surface can become rougher.
Risks of Over-Extrusion, Under-Extrusion, Stringing, and Blobs
Lower layer heights come with a higher risk of over-extrusion, stringing (stray filament strands), and blobs (bulges of excess material). These issues can negatively impact the print’s aesthetics and require post-processing to rectify.
On the other hand, higher layer heights minimize the risks of under-extrusion, gaps, and holes. While the print may lack intricate details, it can be suitable for functional parts that do not require a high level of visual accuracy.
Summary
Choosing the right layer height for your 3D prints involves a trade-off between print detail, surface smoothness, filament usage, printing time, and overall print appearance. Consider the specific requirements of your project and determine the level of detail and smoothness necessary for your desired outcome. Additionally, consider the potential risks associated with each layer height option and the impact they have on the print’s appearance.
Troubleshooting layer height issues and other considerations
Sometimes, issues related to layer height may arise during the printing process. These issues can include inconsistent layers, elephant foot, or layer shifting.
Inconsistent layers can be caused by various factors such as a dirty nozzle, bent Z-axis rod, faulty Z-axis motor or sensor, or incorrect Z-offset value. To troubleshoot this, we recommend the following:
- Clean or replace the nozzle
- Adjust the Z-axis rod
- Check or replace the Z-axis motor or sensor
- Adjust the Z-offset value
Elephant foot, characterized by a flared or widened base, can be caused by factors like high initial layer height, high bed temperature, low cooling fan speed, or excessive bed adhesion. To address this issue, we suggest the following troubleshooting steps:
- Lower the initial layer height
- Reduce the bed temperature
- Increase the cooling fan speed
- Adjust the bed adhesion
Layer shifting, where the layers are not aligned properly, can occur due to high printing speed, acceleration or jerk settings, low belt tension, or a loose or jammed pulley. To prevent layer shifting, consider the following troubleshooting measures:
- Lower the printing speed
- Adjust the acceleration or jerk settings
- Tighten the belts
- Check or lubricate the pulleys
Remember, when selecting the appropriate nozzle and layer height, there is an interdependent relationship. The nozzle diameter determines the maximum effective layer height. Using a nozzle larger than the desired layer height can negatively impact print quality or result in failed prints.
Furthermore, consider other factors such as the intricacy of your model and the desired surface finish. These factors may influence layer height choices beyond the recommendations of your slicer software.
It’s important to note that troubleshooting layer height issues is just one aspect of achieving optimal print quality. Post-processing techniques and throughput optimization should also be taken into consideration to further enhance your prints.
For more in-depth information on troubleshooting layer height issues and optimizing your 3D printing process, support us at www.devilndove.com or visit our store at www.devilndove.online.
Layer Height Issue | Possible Causes | Troubleshooting Steps |
---|---|---|
Inconsistent Layers | Dirty nozzle Bent Z-axis rod Faulty Z-axis motor or sensor Incorrect Z-offset value |
Clean or replace the nozzle Adjust the Z-axis rod Check or replace the Z-axis motor or sensor Adjust the Z-offset value |
Elephant Foot | High initial layer height High bed temperature Low cooling fan speed Excessive bed adhesion |
Lower the initial layer height Reduce the bed temperature Increase the cooling fan speed Adjust the bed adhesion |
Layer Shifting | High printing speed Acceleration or jerk settings Low belt tension Loose or jammed pulley |
Lower the printing speed Adjust the acceleration or jerk settings Tighten the belts Check or lubricate the pulleys |
Conclusion
Adjusting the layer height is a crucial aspect of optimizing your 3D printing process. By considering various factors, troubleshooting common issues, and making informed choices, you can achieve better print quality, speed, and strength.
To ensure optimal results, it is important to calibrate your extruder and bed. This will help maintain consistency in layer height and improve overall print accuracy.
Additionally, utilizing layer height calculators or adaptive layer height options can aid in fine-tuning your settings. These tools take into account factors such as model intricacy and desired surface finish, allowing for customized layer height adjustments beyond the recommendations of slicer software.
Don’t forget to use helpful tools like layer indicators, dial indicators, and feeler gauges to accurately measure and adjust your layer height. These tools will provide you with precise control over your prints and help you achieve the desired results.
By mastering the art of layer height adjustment in 3D printing and implementing these techniques and tools, you can optimize your prints for exceptional quality and take your 3D printing projects to the next level.
Support us at www.devilndove.com or visit our store at www.devilndove.online.
FAQ
What is layer height in 3D printing?
Layer height refers to the thickness of each layer that the printer extrudes. It plays a crucial role in the resolution, strength, and appearance of the final print.
How do I adjust the layer height settings in 3D printing?
To adjust the layer height settings, you need to access the print quality or layer resolution options in the slicer software used for 3D printing. Depending on the software, you can choose from preset values or enter a custom value. You can also adjust the initial layer height, which is usually higher than the other layers to improve adhesion and reduce warping.
What factors should I consider when choosing a layer height for my 3D prints?
When selecting a layer height, factors to consider include the level of detail, surface smoothness, filament usage, printing time, print appearance, and risks of over-extrusion, stringing, blobs, under-extrusion, gaps, and holes.
How can I troubleshoot common layer height issues in 3D printing?
Common layer height issues can include inconsistent layers, elephant foot, and layer shifting. Troubleshooting these issues may involve cleaning or replacing the nozzle, adjusting the Z-axis rod, checking or replacing the Z-axis motor or sensor, adjusting the Z-offset value, lowering the initial layer height, reducing the bed temperature, increasing the cooling fan speed, adjusting the bed adhesion, lowering the printing speed, adjusting the acceleration or jerk settings, tightening the belts, or checking and lubricating the pulleys.
Is the nozzle size important for layer height adjustments?
Yes, the nozzle diameter determines the maximum effective layer height. Using a nozzle larger than the desired layer height can negatively impact print quality or result in failed prints.
Are there considerations beyond slicer software recommendations for layer height adjustments?
Yes, other considerations include model intricacy, desired surface finish, post-processing requirements, and optimizing for throughput if printing speed is a bottleneck.
Source Links
RELATED POSTS
View all